Hardness and processing method of molybdenum
The color of molybdenum is silver gray, and its chemical properties are approximate to tungsten. The hardness of molybdenum is not high (HB35~125), but the hardness of molybdenum material is high. Its brittleness is high at room temperature, when the temperature reached 350℃~450 ℃, the plastic will be increased significantly, but its hardness will also be decreased.
The yield ratio of molybdenum is high. The hardening trend of the machine work is serious. Molybdenum has high elastic modulus (343350 MPa), cutting deformation consumed work much, and cutting force is strong. Molybdenum and tool materials have strong adhesion. Cutting tools are easy to produce the adhesive wear. So cut the molybdenum and its alloys, you should choose these tool materials with enough strength and toughness, good wear resistance, anti bonding, such as YW1, YW2 etc. And if cut molybdenum ingots and sintered bar, you can use the cemented carbide with high intensity of YG6, YG8, YS2 (YGl0H) and other grades.
When cut the molybdenum and molybdenum alloys, you'd better make a sharp cutting edge under the condition of guarantee of the cutter head strength. In the choice of geometric parameters of cutting tool, you can choose the larger rake angle, smaller lead angle, and the negative edge inclination angle. General choice: gamma O=15° ~20°O=10°~12°of alpha kappa r=45°r=15°s=-5° lambda gamma O1=-2°~-5°, B gamma =0.1~0.3mm. Chip curling groove radius Rn=6~8mm, front and back surface roughness Ra is less than or equal to 0.4 M.
In order to keep certain tool durability, you should avoid the high cutting temperature. When you cut molybdenum and its alloys, you should choose the lower cutting speed, the larger cutting depth and the amount of feed. The reference of the cutting dosage: rough car: V C=35~75m/min, ap=4~7mm, f=0.2~0.5mm/r; semi finish turning V C=50~120m/min, ap=0.2~0.4mm, f=0.15~0.4, mm/r.
The cutting of molybdenum and its alloys should pay full attention to the cooling lubrication, the miscible liquids of CC14 added No. 20 oil or MoS2 can be as the lubricating oil (grease), but CC14 has toxic and corrosive effect, so the protective measures should be taken when you use it.
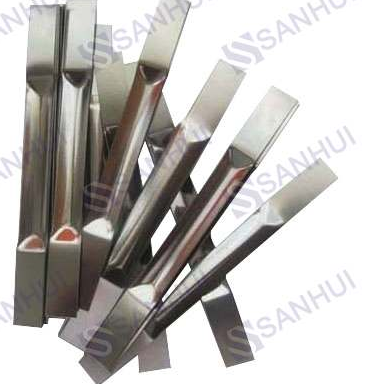
The yield ratio of molybdenum is high. The hardening trend of the machine work is serious. Molybdenum has high elastic modulus (343350 MPa), cutting deformation consumed work much, and cutting force is strong. Molybdenum and tool materials have strong adhesion. Cutting tools are easy to produce the adhesive wear. So cut the molybdenum and its alloys, you should choose these tool materials with enough strength and toughness, good wear resistance, anti bonding, such as YW1, YW2 etc. And if cut molybdenum ingots and sintered bar, you can use the cemented carbide with high intensity of YG6, YG8, YS2 (YGl0H) and other grades.
When cut the molybdenum and molybdenum alloys, you'd better make a sharp cutting edge under the condition of guarantee of the cutter head strength. In the choice of geometric parameters of cutting tool, you can choose the larger rake angle, smaller lead angle, and the negative edge inclination angle. General choice: gamma O=15° ~20°O=10°~12°of alpha kappa r=45°r=15°s=-5° lambda gamma O1=-2°~-5°, B gamma =0.1~0.3mm. Chip curling groove radius Rn=6~8mm, front and back surface roughness Ra is less than or equal to 0.4 M.
In order to keep certain tool durability, you should avoid the high cutting temperature. When you cut molybdenum and its alloys, you should choose the lower cutting speed, the larger cutting depth and the amount of feed. The reference of the cutting dosage: rough car: V C=35~75m/min, ap=4~7mm, f=0.2~0.5mm/r; semi finish turning V C=50~120m/min, ap=0.2~0.4mm, f=0.15~0.4, mm/r.
The cutting of molybdenum and its alloys should pay full attention to the cooling lubrication, the miscible liquids of CC14 added No. 20 oil or MoS2 can be as the lubricating oil (grease), but CC14 has toxic and corrosive effect, so the protective measures should be taken when you use it.
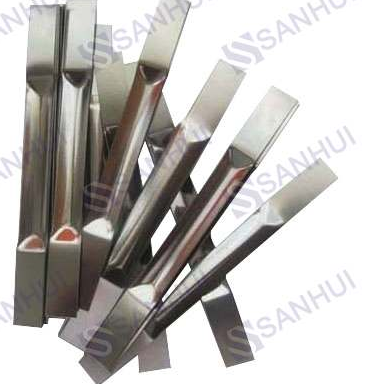