The big summary about the broken wire of molybdenum wire
1. Broken wire associated with molybdenum wire
(1). Tension and wire speed
A. Improve the molybdenum wire tension can reduce the influence of wire vibration, and then the precision and cutting speed will be improved, the wire breaking will also be obviously reduced. In general, the tension in 12-15N is regarded as appropriate.
B. The improvement of the wire speed can help molybdenum wire take the working fluid into the larger thickness of workpiece, and make the electric corrosion product love shooting and electrical discharge machining stability. But the wire speed is too high, the shaking of molybdenum wire is serious. This will damage the stability of machining. In addition, the machining accuracy and surface roughness will become worse, and easy to cause the broken wire. If the wire speed is too low, it is also easy to cause the broken wire because of the big loss, generally, experience of less than 10ms is appropriate.
(2)The thick workpiece generally refers to the workpiece whose thickness is greater than 100mm. The main reasons for broken wire are as follows:
A. Cutting the starting broken wire
This is due to the initial cutting, molybdenum wire on the workpiece, the upper and lower guide wheel drive away from large, this will cause the molybdenum wire pulling jitter, so that the gap is unstable between the molybdenum wire and the workpiece, and it is easy to form the arc discharge, the arc is concentrated on a segment, it will cause the broken wire. In EDM, the arc discharge is the main factors that cause the anode corrosion damage.
2. The broken wire in the cutting process
When the molybdenum wire is put into the workpiece, because the narrow kerfs, emulsion is difficult to infiltrate, cutting electric corrosion products (carbon black and metal) in the gap is not easy to remove, this will make the processing conditions deteriorate, in the generation of electrical discharge machining two times, three times the slit, resulting in variable width, therefore, the gap will go into the poor state the pulse forming, arc discharge, caused by the fault of silk.
3. The broken wire at the end of cutting
When the cutting is nearly finished, the broken wire with a few millimeters, even tens of microns appeared. Except for the above reasons, the reason of this broken wire is that the weight of workpiece or the internal stress of workpiece material. The solution measure is: The material factory should make a necessary heat treatment before processing.
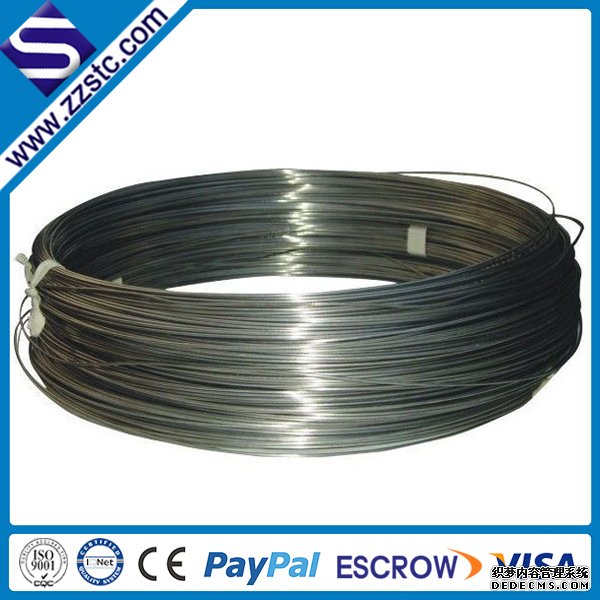
(1). Tension and wire speed
A. Improve the molybdenum wire tension can reduce the influence of wire vibration, and then the precision and cutting speed will be improved, the wire breaking will also be obviously reduced. In general, the tension in 12-15N is regarded as appropriate.
B. The improvement of the wire speed can help molybdenum wire take the working fluid into the larger thickness of workpiece, and make the electric corrosion product love shooting and electrical discharge machining stability. But the wire speed is too high, the shaking of molybdenum wire is serious. This will damage the stability of machining. In addition, the machining accuracy and surface roughness will become worse, and easy to cause the broken wire. If the wire speed is too low, it is also easy to cause the broken wire because of the big loss, generally, experience of less than 10ms is appropriate.
(2)The thick workpiece generally refers to the workpiece whose thickness is greater than 100mm. The main reasons for broken wire are as follows:
A. Cutting the starting broken wire
This is due to the initial cutting, molybdenum wire on the workpiece, the upper and lower guide wheel drive away from large, this will cause the molybdenum wire pulling jitter, so that the gap is unstable between the molybdenum wire and the workpiece, and it is easy to form the arc discharge, the arc is concentrated on a segment, it will cause the broken wire. In EDM, the arc discharge is the main factors that cause the anode corrosion damage.
2. The broken wire in the cutting process
When the molybdenum wire is put into the workpiece, because the narrow kerfs, emulsion is difficult to infiltrate, cutting electric corrosion products (carbon black and metal) in the gap is not easy to remove, this will make the processing conditions deteriorate, in the generation of electrical discharge machining two times, three times the slit, resulting in variable width, therefore, the gap will go into the poor state the pulse forming, arc discharge, caused by the fault of silk.
3. The broken wire at the end of cutting
When the cutting is nearly finished, the broken wire with a few millimeters, even tens of microns appeared. Except for the above reasons, the reason of this broken wire is that the weight of workpiece or the internal stress of workpiece material. The solution measure is: The material factory should make a necessary heat treatment before processing.
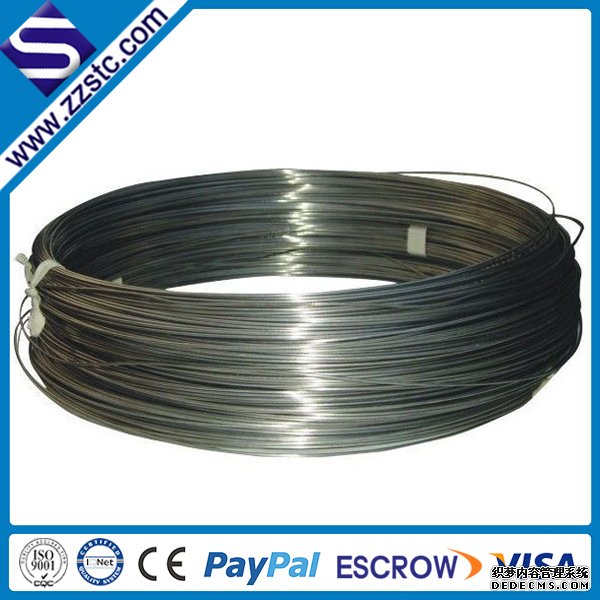